Maximizing Performance with Rubber Gaskets
Maximizing performance with rubber gaskets involves selecting the right gasket material, design, and installation techniques for your specific application. Rubber gaskets are commonly used for sealing and insulation purposes in various industries. Here’s how you can ensure optimal performance with rubber gaskets:
- Material Selection:
- Choose the appropriate rubber material based on the requirements of your application. Consider factors like temperature resistance, chemical compatibility, and environmental conditions. Common rubber materials include neoprene, EPDM, silicone, and nitrile, among others.
- Customization:
- If standard gaskets do not fully meet your needs, consider customizing gaskets to match the exact specifications of your application. Custom gaskets can be designed to fit the unique shape and size requirements of your equipment.
- Proper Design:
- Ensure that the design of the gasket, including dimensions, thickness, and shape, is appropriate for your specific application. Gaskets should be designed to create an effective seal without overcompression.
- Tolerance Control:
- Pay attention to tolerance control during the manufacturing process to ensure the gaskets are produced with precision. This helps maintain the right fit and sealing properties.
- Quality Assurance:
- Source gaskets from reputable manufacturers who have stringent quality control processes in place. Quality assurance ensures that the gaskets meet industry standards and perform reliably.
- Proper Installation:
- Follow the manufacturer’s installation guidelines for your gaskets. Proper installation includes using the correct torque values and tightening procedures to create a secure and effective seal.
- Surface Preparation:
- Ensure that the mating surfaces are clean, smooth, and free from debris, rust, or imperfections. Proper surface preparation is essential for gaskets to seal effectively.
- Alignment:
- Align the gasket and the flanges correctly during installation. Misalignment can lead to uneven compression and potential leaks.
- Tightening Sequence:
- Follow the recommended tightening sequence when securing the gasket. This ensures even compression and a consistent seal.
- Bolting and Torque Values:
- Use the appropriate bolting and torque values as specified in the gasket manufacturer’s instructions. Over-tightening can damage the gasket, while under-tightening can lead to leaks.
- Inspection and Maintenance:
- Regularly inspect the gaskets for wear, damage, or degradation. Replace gaskets as needed to maintain peak performance and prevent leaks.
- Environmental Considerations:
- Consider the environmental factors that may impact gasket performance. For instance, extreme temperatures or exposure to chemicals may require specific gasket materials and designs.
- Testing and Validation:
- In critical applications, consider conducting leak testing or pressure testing to validate the performance of the gaskets under actual operating conditions.
By carefully considering these factors and following best practices, you can maximize the performance of rubber gaskets in your specific application, ensuring a reliable and effective sealing solution.
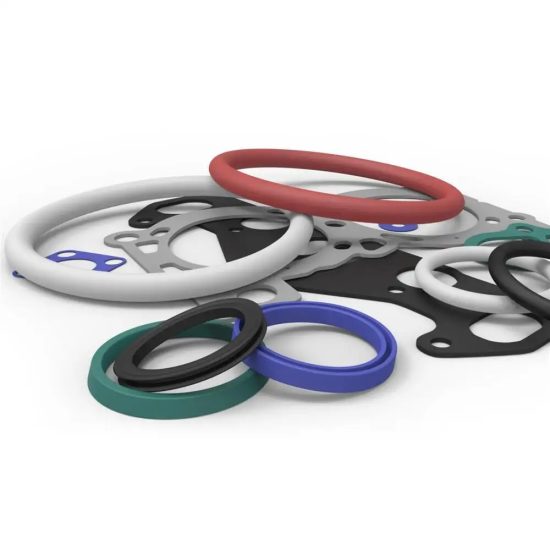
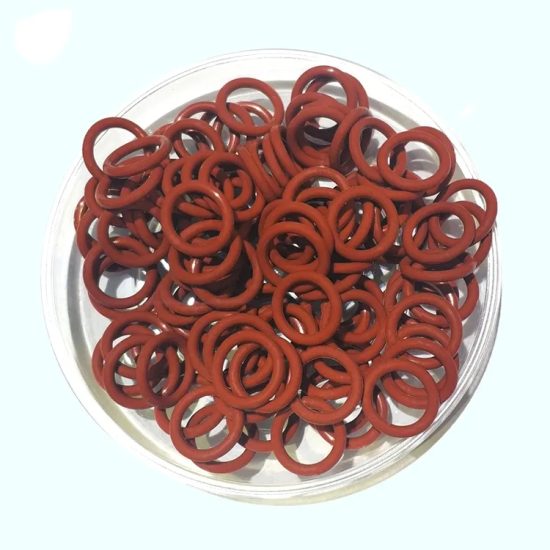